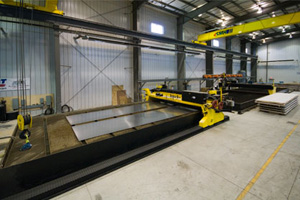
Waterjet cutters are one of the top competing choices for precision cutting methods. The devices are capable of the same cutting tasks as plasma cutting machines and laser cutters, while also producing no heat affected zones (HAZ). Waterjet cutters assume many characteristics that give them an advantage over typical precision cutting methods. For instance, the ability to work with various densities makes them ideal for composite cutting, and waterjet cutters are recognized as "green” technologies.
Waterjet cutting systems have been around since the 1970's. However, the conception of waterjet cutters began about twenty years prior.
The process of waterjet systems can be dated back to the 1950's. It began with the forestry engineer, Dr. Norman Franz who had been researching the use of extremely pressurized water as a means of cutting trees for lumber. While not responsible for commercial use of waterjet cutters, Franz did prove the effectiveness of quick flowing and high pressure water as a cutting device.
Commercial waterjet systems did not appear until the 1970's. Early versions were very costly and required a great deal of maintenance. However, compared to other methods of the time, waterjet cutters were one of the more affordable options.
Early waterjet were what are now called pure waterjet cutting machines. Pure waterjets use plain, but highly pressurized and rapid moving water to cut materials. These devices cut softer materials such as:
-
Foam
-
Plastic
-
Rubber
-
Cardboard
-
Leather
-
Food products
-
Paper
The 1980's saw the introduction of abrasive waterjet cutting machines. In abrasive waterjet systems, the same process used in pure waterjet systems is employed. However, rather than using plain water, abrasive systems use a combination of water and abrasives such as garnet, making these machines better for tougher materials. Examples of materials used for abrasive systems include:
-
Marble
-
Metal
-
Granite
-
Wood
-
Stone
-
Ceramic
In abrasive waterjet machines, the abrasive particles are drawn into the rapid stream and are mixed together in the mixing tube, or mixing chamber. This common version of abrasive waterjet systems is called entrainment. Entrained waterjet machines are preferred over slurry waterjet machines -- another form of abrasive waterjets.
Slurry waterjet systems are subject to frequent wear as the abrasives are mixed with the water before it is pressurized. The mixing of abrasives and water is not designated to specific area like the mixing tube, causing the equipment to deteriorate as the solution travels throughout the entire system.
All variations of waterjet cutting machines use extremely narrow nozzle openings to produce pressures anywhere from 40,000 pounds per square inch (psi), to 60,000 psi. The water flows as quickly as around 2,500 feet a second and the diameter of the stream is as narrow as 0.005 inches (or 1 millimeter).
The first industry to begin using abrasive waterjet machines was the space industry and aviation industry. Today, waterjet cutters are more frequently used within an assortment of industries due to the many benefits these machines provide.